Analysis of Loosening and Falling-off of Hexagonal Roller of Pipe Belt Machine
Release time:
Mar 27,2020
For the structure of the hexagonal idler group mentioned in this article, please refer to the description of the structure of the pipe idler bracket with adjusting structure in the field. In the structure, the shaft end of the idler is not connected with the bracket by a buckle, but is connected by a screw. Description of 2. problems 1. During the installation and debugging stage, the idler was loose and some screws fell off, as shown in the following figure: 2. During the normal operation stage, the maintenance personnel did not find the looseness in time and the idler fell off completely. 3. The main problem is that there are potential safety hazards, especially the overhead of the pipe belt conveyor is above the pedestrian or motorway. 3. reason analysis 1. The idler began to loosen in the installation and debugging stage. The main reason is that the anti-loosening of the shaft end fixing screw is not in place. According to the illustration of GB/T854 single-ear stop washer, the washer needs to be bent twice after installation, as shown in the following figure. However, in most cases on site, the arc bending edge is not bent, or even if it is bent, the bending edge is not stuck on the hexagon of the hexagon nut as required. The following figure shows the situation that the arc bending edge is not folded: the following figure shows the situation that the arc bending edge is not folded in place: 2. The main reason for the drop of the trusteeship in the normal operation stage is that the stop gasket has not taken anti-corrosion measures, and the corrosion will fail after a period of operation. For example, the stop gasket in the above picture has been rusted. In addition, the anti-corrosion rust of the set screw at the shaft end and the mounting bolt of the roller bracket is also the cause of the roller falling after long-term operation. 4. solution 1. From the design point of view, the stop gasket cannot be less, and the stop gasket must adopt measures with high anti-corrosion performance such as galvanizing, and the fastening screw is the same. In addition, from the perspective of prevention, the bottom of the truss can be added with a protective net or closed steel plate for the pre-idler to fall. 2. From the installation angle, the two bends of the stop gasket must be in place and cannot be careless. After a section of truss idler is installed, the whole section shall be inspected. 3. From the perspective of operation and maintenance, on-site maintenance and repair personnel shall regularly check the condition of the idler and find the looseness of the idler in time to avoid the risk of the idler falling at any time. 5. other instructions 1. If the above solution is followed, the incident of the idler falling and hitting people can be completely eliminated, and there is no need to worry too much about it. 2. The protective steel plate or steel wire mesh added at the bottom of the truss must be well protected against corrosion. The thickness of the steel plate is more than 2mm, and the steel wire mesh shall be galvanized mesh with an aperture of not more than 10mm and a steel wire diameter of not less than 2mm. 3. For the pipe belt conveyor with a long distance, it is impossible to ensure that the stop gasket during the installation of the idler is 100% installed in place. During the installation and debugging phase, the installer or on-site technical personnel shall check back and forth to ensure that the risk is minimized. 4. If the object falls due to other reasons, such as tube expansion or belt torsion, the best protective measure is to add closed steel plate, but it should be cleaned up in time after the accident.
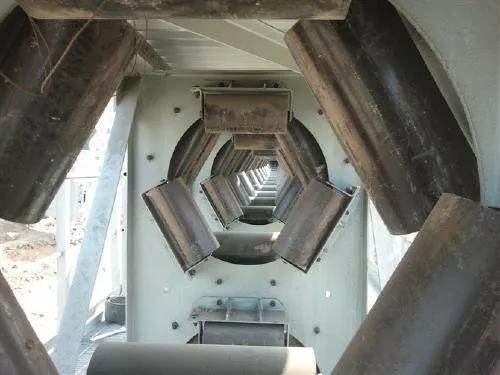
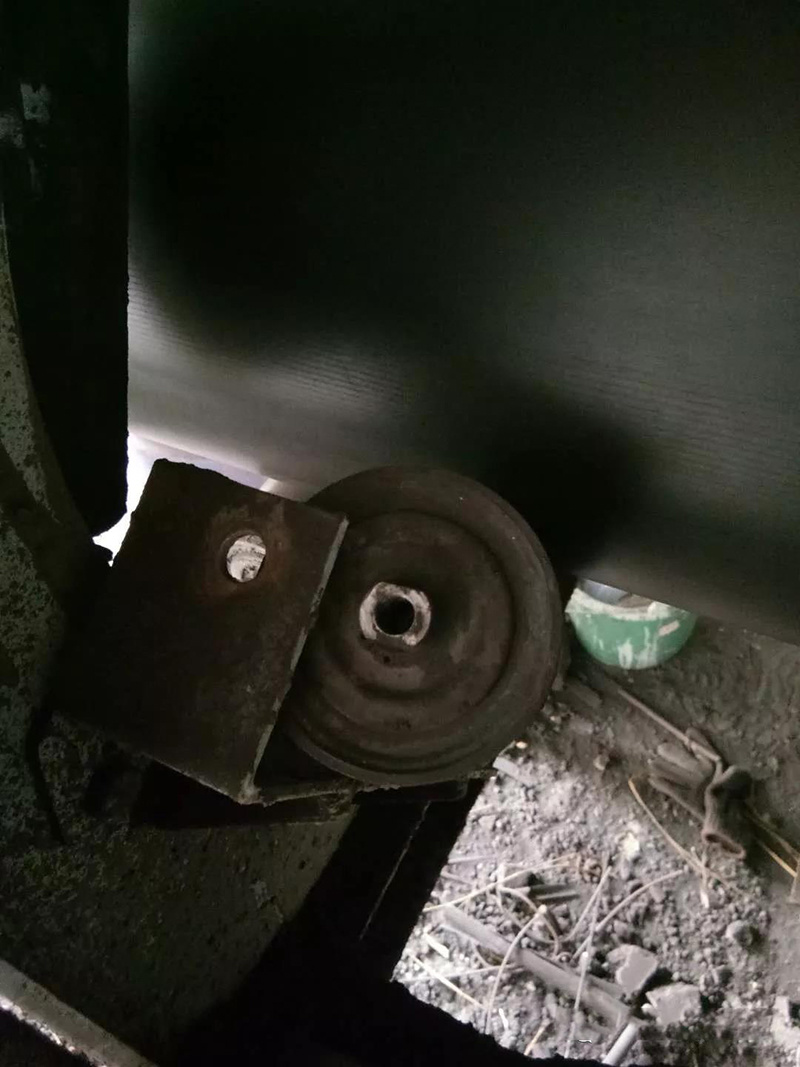
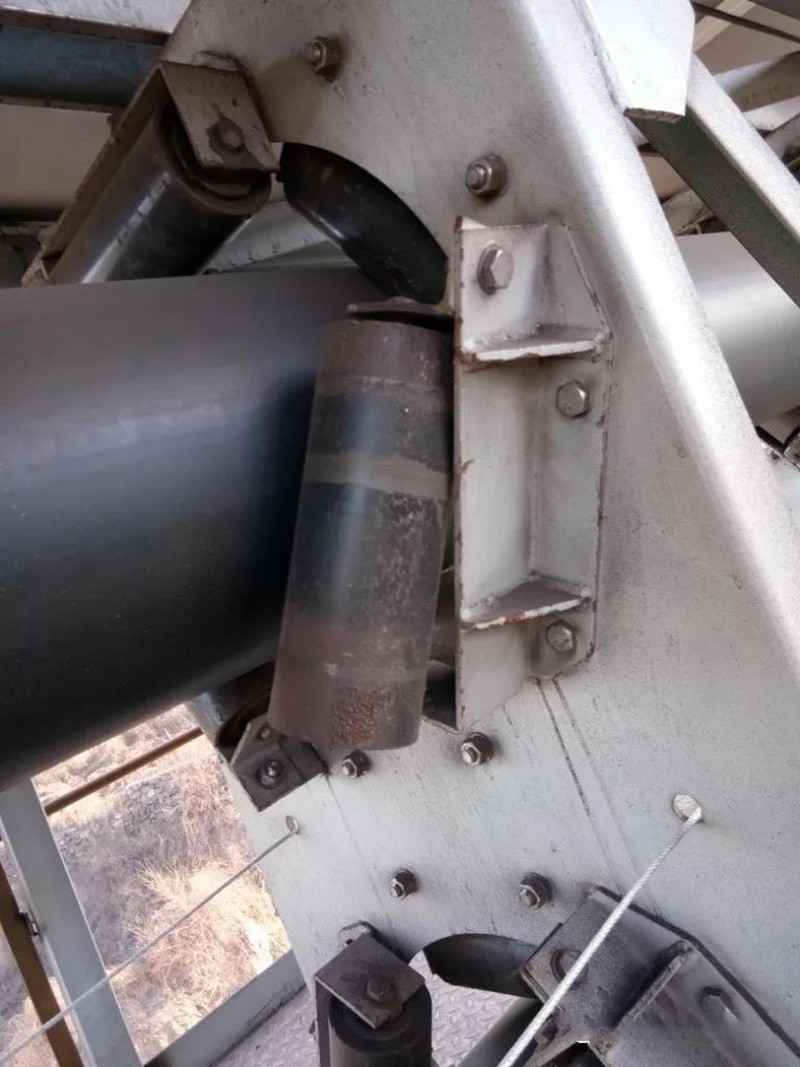
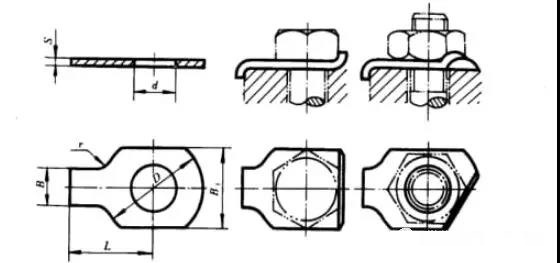
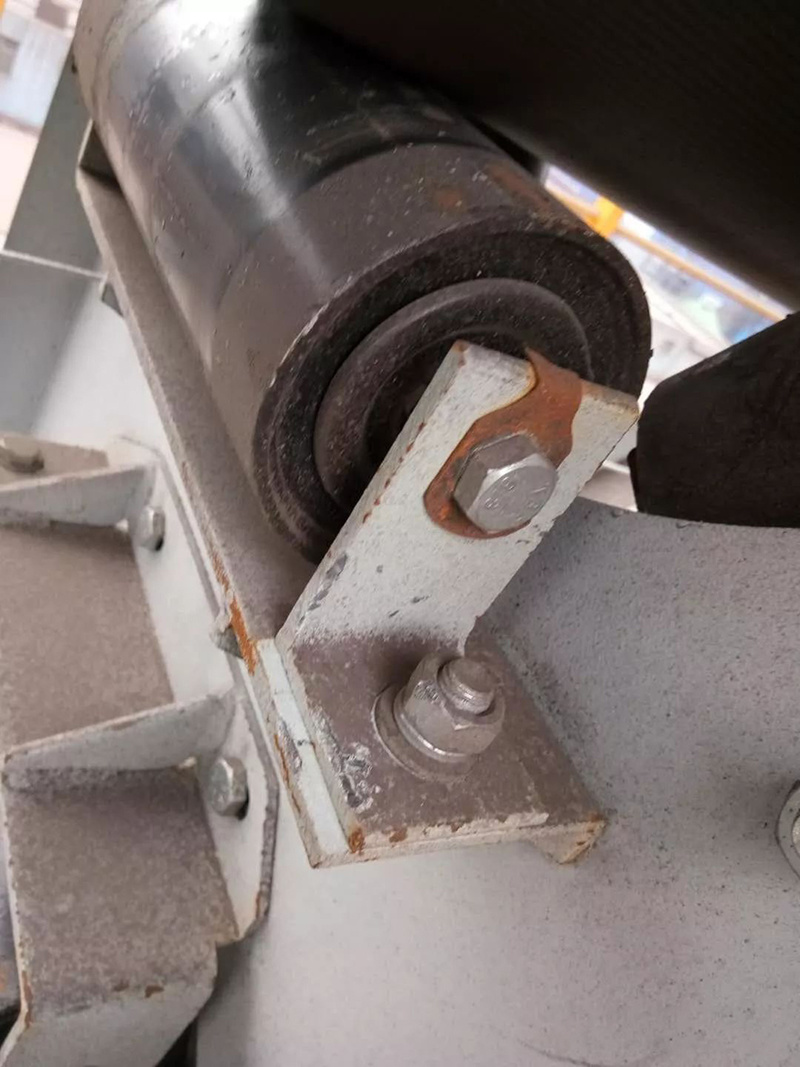
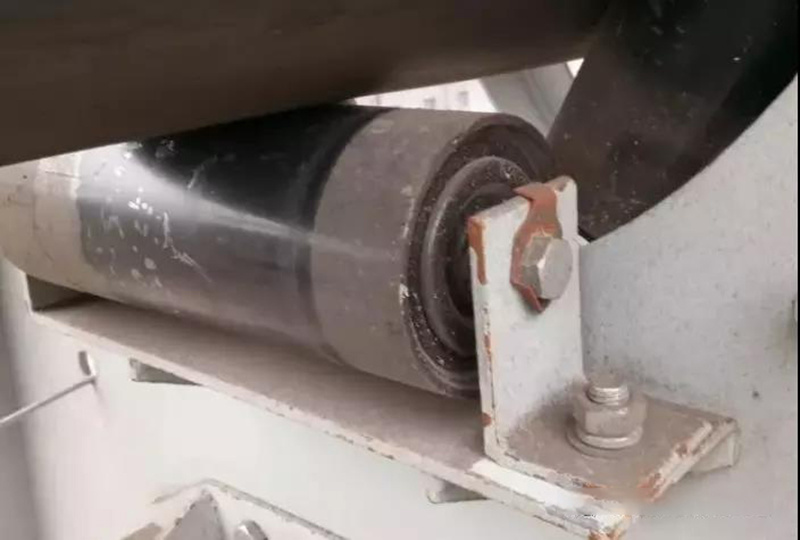
Key words:
Next Page
Next page:
Recommended News
HUADONG Machinery
Add: No.8, Yanghuan Road, High-tech zone, Jiangyin, Jiangsu, China
Tel: 86-510-86195578
Mobile: 86-15190313883 86-18762809313
E-mail: sales@hdconveyor.com
Official Website
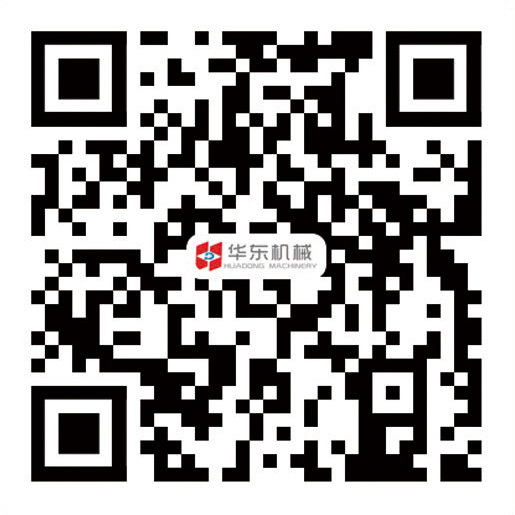